Model NO.: YN-1325XYC
Color: Customed
Main Markets: Europe, USA, Middle East, Southeast Asia
Delivery Detail: 3 Days Delivery
Keyword: SPA Vacuum Forming Machine
Package: Plywood Case
Trademark: YN
Transport Package: Plywood Case
Specification: 1200*2400*200mm
Origin: Shandong, China
HS Code: 8477401000
Model NO.: YN-1325XYC
Color: Customed
Main Markets: Europe, USA, Middle East, Southeast Asia
Delivery Detail: 3 Days Delivery
Keyword: SPA Vacuum Forming Machine
Package: Plywood Case
Trademark: YN
Transport Package: Plywood Case
Specification: 1200*2400*200mm
Origin: Shandong, China
HS Code: 8477401000
          China newest acrylic bathtub/spa vacuum forming machine
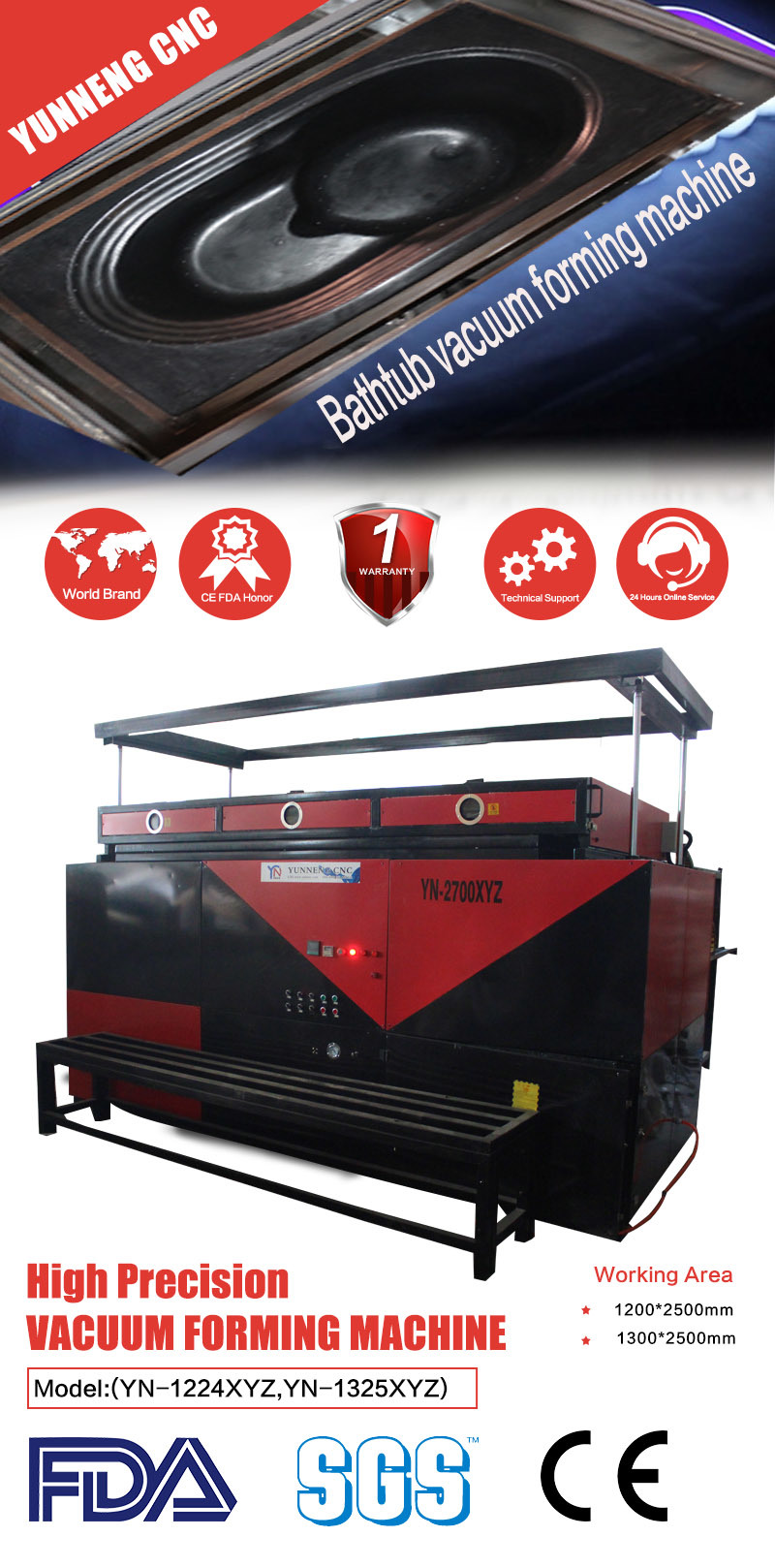
Â
 Acrylic Vacuum Forming Machine Technical Parameter |
Model |
YN-1400X |
YN-2700XY |
YN-3020XY |
YN-3700XYC |
Working area (mm) |
1320x1320 |
2620x1320 |
3100x2100 |
3620x2100 |
Total power (kw) |
8 |
16 |
24 |
32 |
Suction holes |
1 |
3 |
3 |
3 |
Heating area |
1 |
2 |
2 |
2 |
Case coating |
Electrostatic spray |
Electrostatic spray |
Electrostatic spray |
Spray painting |
Open Method |
Manual open/ Pneumatic open |
Manual open/ Pneumatic open |
Manual open/ Pneumatic open |
Sliding open |
Voltage(V) |
AC380/50-60HZ or 220v/1p |
AC380/50-60HZ |
AC380/50-60HZ |
AC380/50-60HZ |
Overall size  (mm)  |
1500*1500*1250 |
2750*1500*1250 |
3190*2200*1250 |
3820*2200*1250 |
Weight (kgs) |
350 |
550 |
1200 |
1800 Â |
Â
Â
1) Making moldsÂ
Â
2) Seal Acrylic sheetÂ
Â
3) Heat and soft Acrylic
Â
4) Suction, molding, cooling
Â
5)Â Trimming
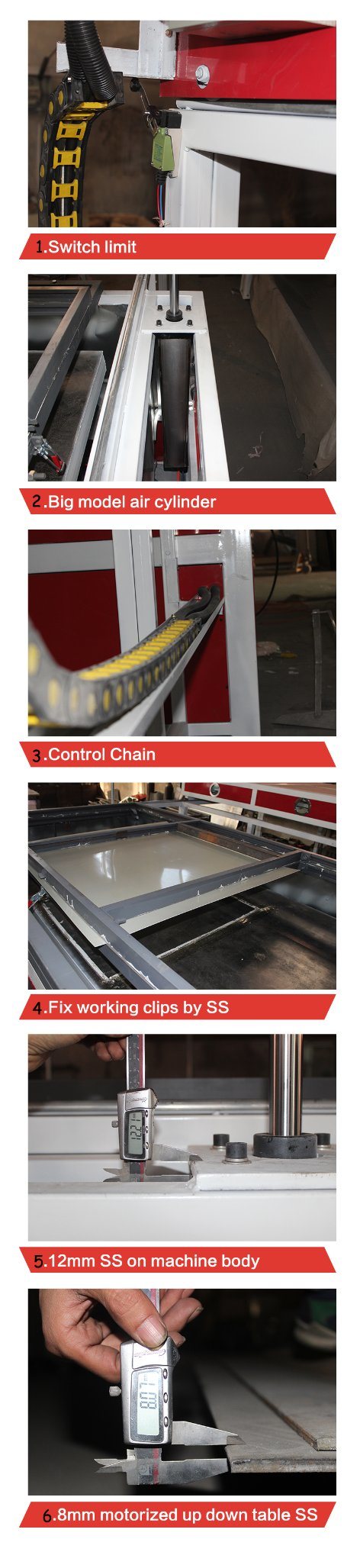
Â
Â
1.This machine has a high power pick-up vacuum pump and large bed size. Custom made heating elements have a life rated at 8-10 thousand hours and can comfortably run 24 hours a day.
Â
2.Working platform is made of steel and has been heat processed preventing distortion and extending the life of the machine.
Â
3.The temperature control is regulated and thermostatically controlled. The entire lid is covered in heat reflective material assisting in heating thus making the unit energy efficient and saving on power.
4.This machine is fully automatic. Simply place your mold inside the cabinet, close the lid and press the button.
Â
5.The machine automatically heats and softens the acrylic to your specified temperature, then engages the pump at the correct temperature and creates the mold all in 1 process.
Â
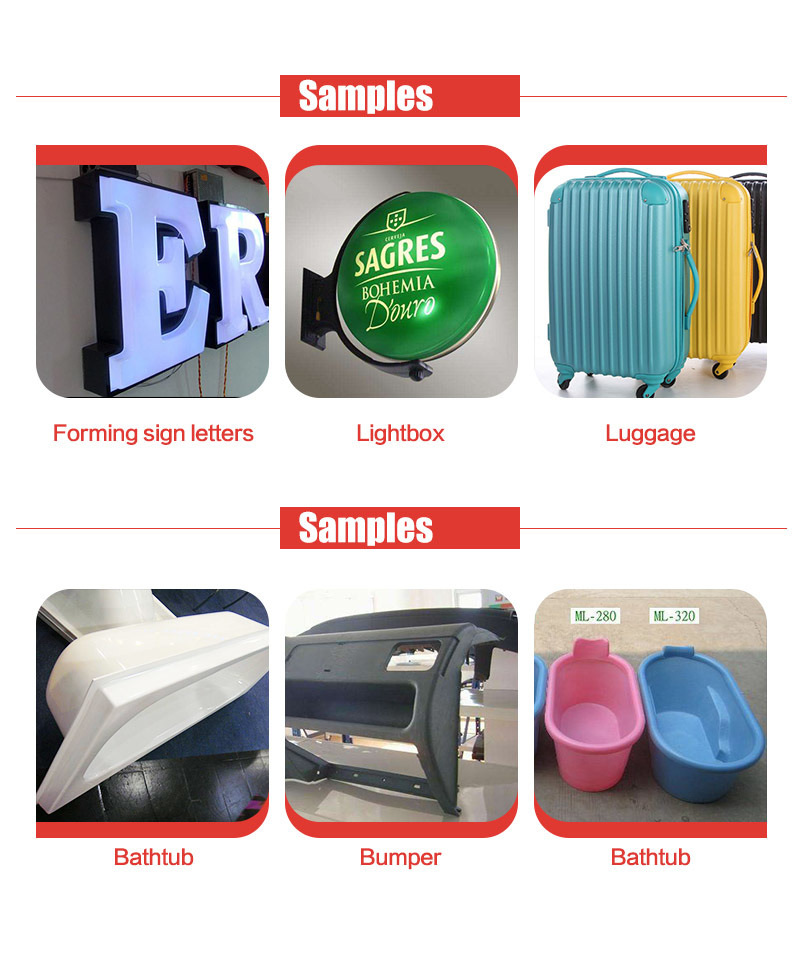
   Weifang Yunneng CNC Equipments Co., Ltd is a new and high technology enterprise in China. Our company is specialized in computer software development and technology transfer, laser equipment. Undertake precise laser processing business.Â
Relying on the China from universities and research institutions, we are the main business agent of the optical equipment such as: metal laser marking machine, laser engraving machine, laser metal cutting machine, laser welding machine, laser die board making machine ,cnc router channel letter bending machine and vacuum forming machine. Our products can be applied to the fields of hardware auto parts, clothing, leathers, toys, electronic appliance, models, process advertising, stones, decorations, plastics, glass industry and others.
         Yunneng  insists on "quality wins the market and the quality service wins the customers". Complying with European CE certification, our products sell well in over 30 countries and regions, such as Brazil, Mexico, Belgium, Iran, Thailand, Korea, Vietnam, the USA, Germany, Italy, Australia, Pakistan, Egypt, Spain, South Africa and Lithuania, etc.
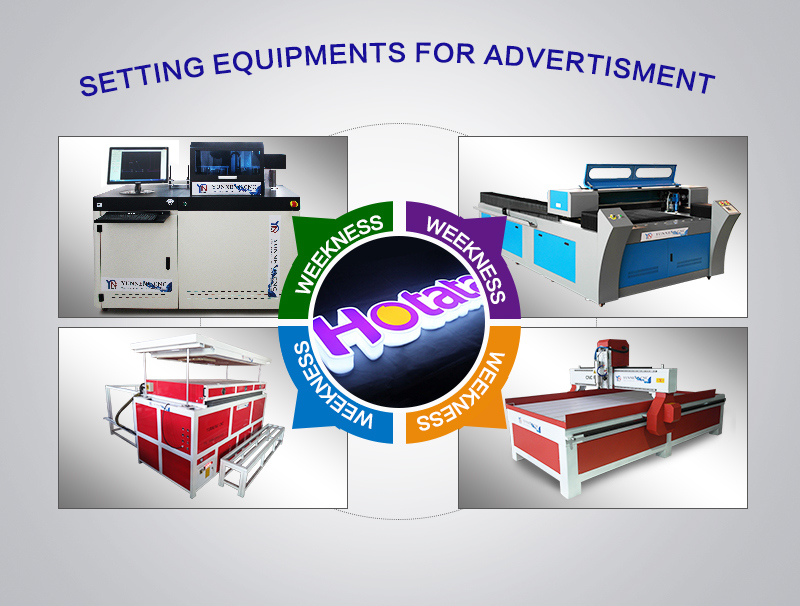
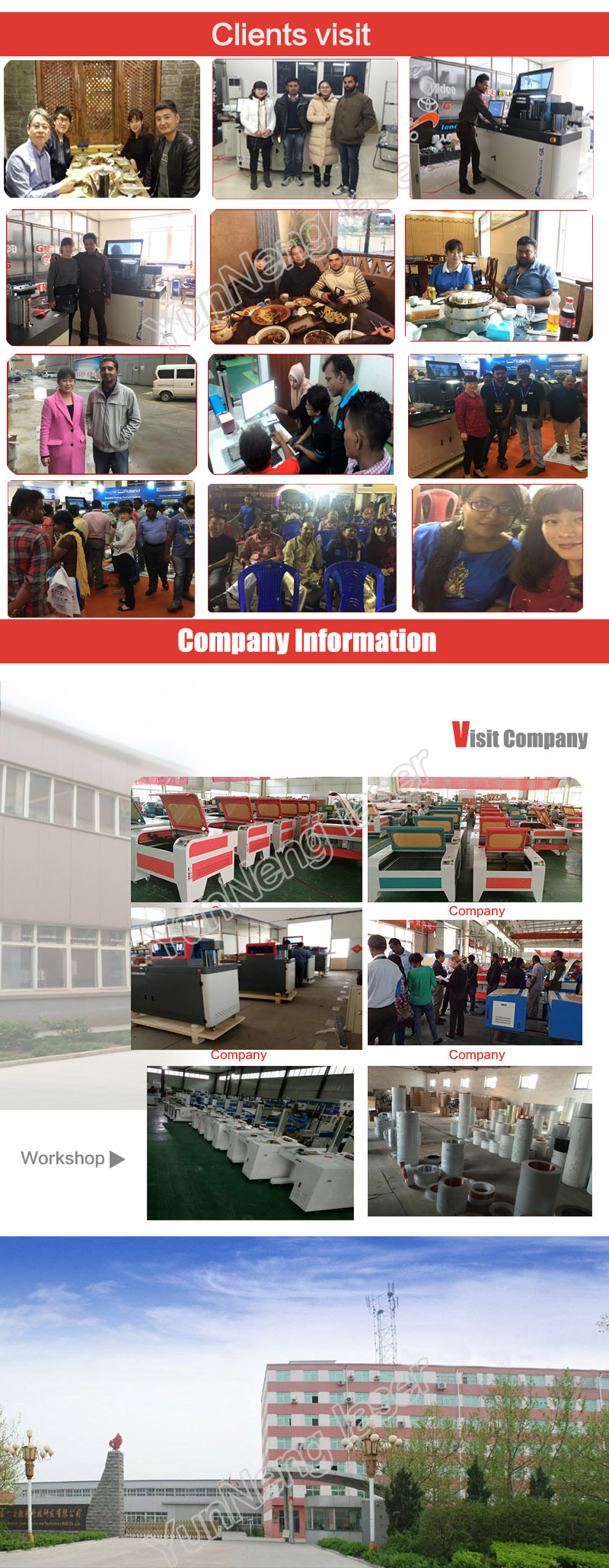
    Thermoforming is a manufacturing process where a plastic sheet is heated to a pliable forming temperature, formed to a specific shape in a mold, and trimmed to create a usable product. The sheet, or "film" when referring to thinner gauges and certain material types, is heated in an oven to a high-enough temperature that permits it to be stretched into or onto a mold and cooled to a finished shape. Its simplified version is vacuum forming.
In its simplest form, a small tabletop or lab size machine can be used to heat small cut sections of plastic sheet and stretch it over a mold using vacuum. This method is often used for sample and prototype parts. In complex and high-volume applications, very large production machines are utilized to heat and form the plastic sheet and trim the formed parts from the sheet in a continuous high-speed process, and can produce many thousands of finished parts per hour depending on the machine and mold size and the size of the parts being formed.
Thermoforming differs from injection molding, blow molding, rotational molding and other forms of processing plastics. Thin-gauge thermoforming is primarily the manufacture of disposable cups, containers, lids, trays, blisters, clamshells, and other products for the food, medical, and general retail industries. Thick-gauge thermoforming includes parts as diverse as vehicle door and dash panels, refrigerator liners, utility vehicle beds, and plastic pallets.
In the most common method of high-volume, continuous thermoforming of thin-gauge products, plastic sheet is fed from a roll or from an extruder into a set of indexing chains that incorporate pins, or spikes, that pierce the sheet and transport it through an oven for heating to forming temperature. The heated sheet then indexes into a form station where a mating mold and pressure-box close on the sheet, with vacuum then applied to remove trapped air and to pull the material into or onto the mold along with pressurized air to form the plastic to the detailed shape of the mold. (Plug-assists are typically used in addition to vacuum in the case of taller, deeper-draw formed parts in order to provide the needed material distribution and thicknesses in the finished parts.) After a short form cycle, a burst of reverse air pressure is actuated from the vacuum side of the mold as the form tooling opens, commonly referred to as air-eject, to break the vacuum and assist the formed parts off of, or out of, the mold. A stripper plate may also be utilized on the mold as it opens for ejection of more detailed parts or those with negative-draft, undercut areas. The sheet containing the formed parts then indexes into a trim station on the same machine, where a die cuts the parts from the remaining sheet web, or indexes into a separate trim press where the formed parts are trimmed. The sheet web remaining after the formed parts are trimmed is typically wound onto a take-up reel or fed into an inline granulator for recycling.
Most thermoforming companies recycle their scrap and waste plastic, either by compressing in a baling machine or by feeding into a granulator (grinder) and producing ground flake, for sale to reprocessing companies or re-use in their own facility. Frequently, scrap and waste plastic from the thermoforming process is converted back into extruded sheet for forming again.
          China newest acrylic bathtub/spa vacuum forming machine
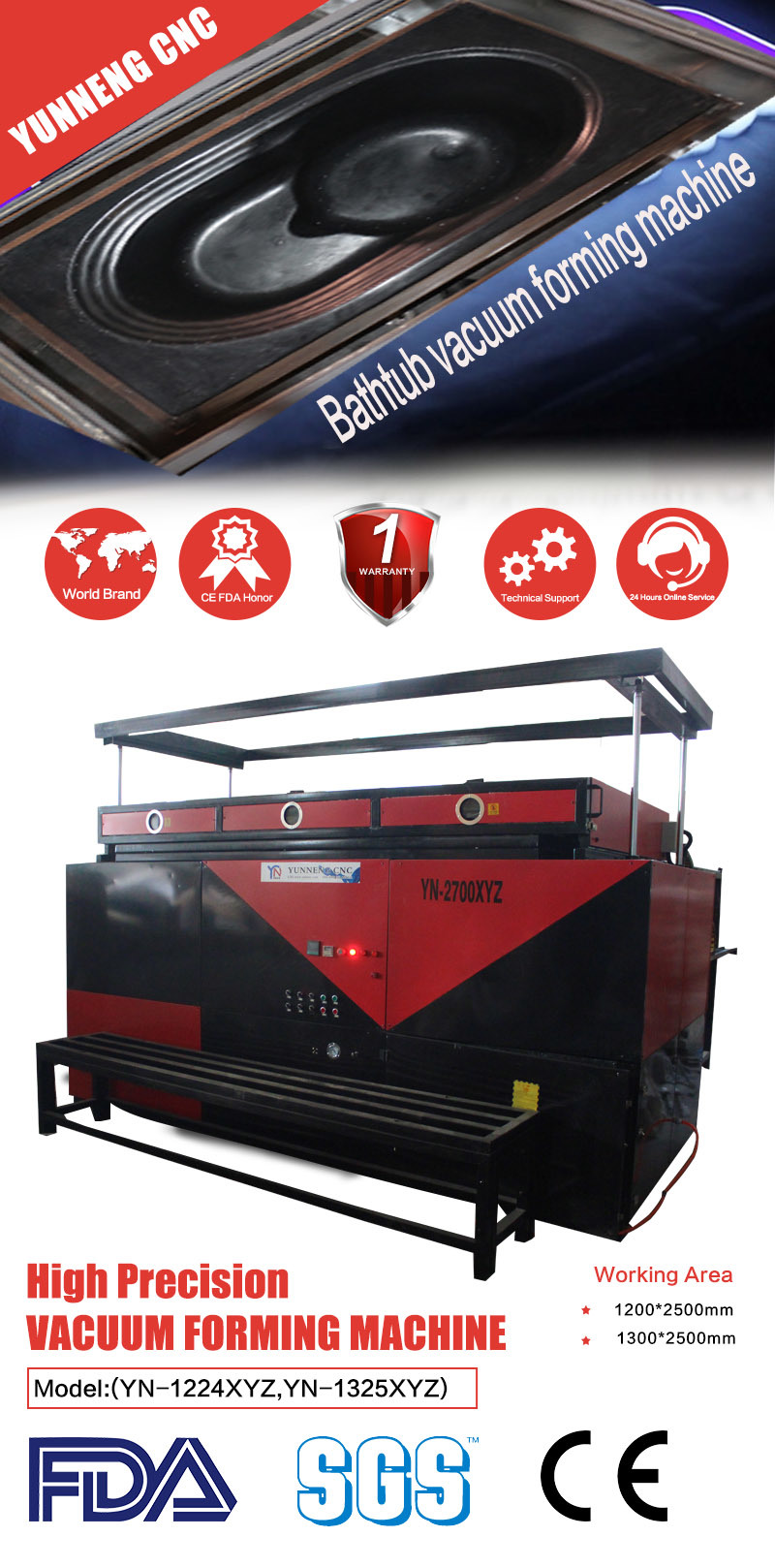
Â
 Acrylic Vacuum Forming Machine Technical Parameter |
Model |
YN-1400X |
YN-2700XY |
YN-3020XY |
YN-3700XYC |
Working area (mm) |
1320x1320 |
2620x1320 |
3100x2100 |
3620x2100 |
Total power (kw) |
8 |
16 |
24 |
32 |
Suction holes |
1 |
3 |
3 |
3 |
Heating area |
1 |
2 |
2 |
2 |
Case coating |
Electrostatic spray |
Electrostatic spray |
Electrostatic spray |
Spray painting |
Open Method |
Manual open/ Pneumatic open |
Manual open/ Pneumatic open |
Manual open/ Pneumatic open |
Sliding open |
Voltage(V) |
AC380/50-60HZ or 220v/1p |
AC380/50-60HZ |
AC380/50-60HZ |
AC380/50-60HZ |
Overall size  (mm)  |
1500*1500*1250 |
2750*1500*1250 |
3190*2200*1250 |
3820*2200*1250 |
Weight (kgs) |
350 |
550 |
1200 |
1800 Â |
Â
Â
1) Making moldsÂ
Â
2) Seal Acrylic sheetÂ
Â
3) Heat and soft Acrylic
Â
4) Suction, molding, cooling
Â
5)Â Trimming
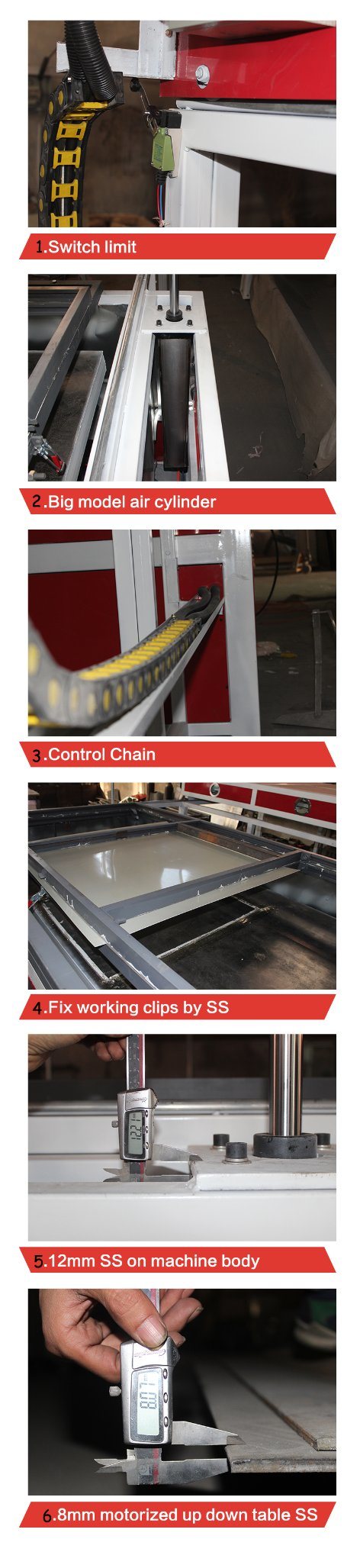
Â
Â
1.This machine has a high power pick-up vacuum pump and large bed size. Custom made heating elements have a life rated at 8-10 thousand hours and can comfortably run 24 hours a day.
Â
2.Working platform is made of steel and has been heat processed preventing distortion and extending the life of the machine.
Â
3.The temperature control is regulated and thermostatically controlled. The entire lid is covered in heat reflective material assisting in heating thus making the unit energy efficient and saving on power.
4.This machine is fully automatic. Simply place your mold inside the cabinet, close the lid and press the button.
Â
5.The machine automatically heats and softens the acrylic to your specified temperature, then engages the pump at the correct temperature and creates the mold all in 1 process.
Â
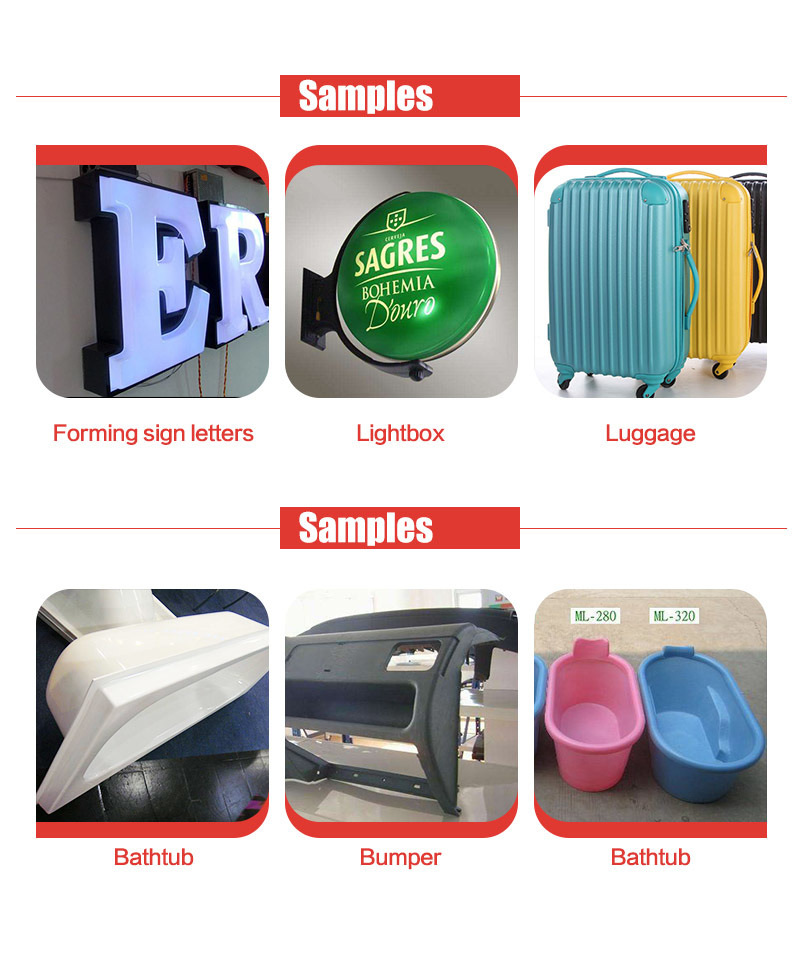
   Weifang Yunneng CNC Equipments Co., Ltd is a new and high technology enterprise in China. Our company is specialized in computer software development and technology transfer, laser equipment. Undertake precise laser processing business.Â
Relying on the China from universities and research institutions, we are the main business agent of the optical equipment such as: metal laser marking machine, laser engraving machine, laser metal cutting machine, laser welding machine, laser die board making machine ,cnc router channel letter bending machine and vacuum forming machine. Our products can be applied to the fields of hardware auto parts, clothing, leathers, toys, electronic appliance, models, process advertising, stones, decorations, plastics, glass industry and others.
         Yunneng  insists on "quality wins the market and the quality service wins the customers". Complying with European CE certification, our products sell well in over 30 countries and regions, such as Brazil, Mexico, Belgium, Iran, Thailand, Korea, Vietnam, the USA, Germany, Italy, Australia, Pakistan, Egypt, Spain, South Africa and Lithuania, etc.
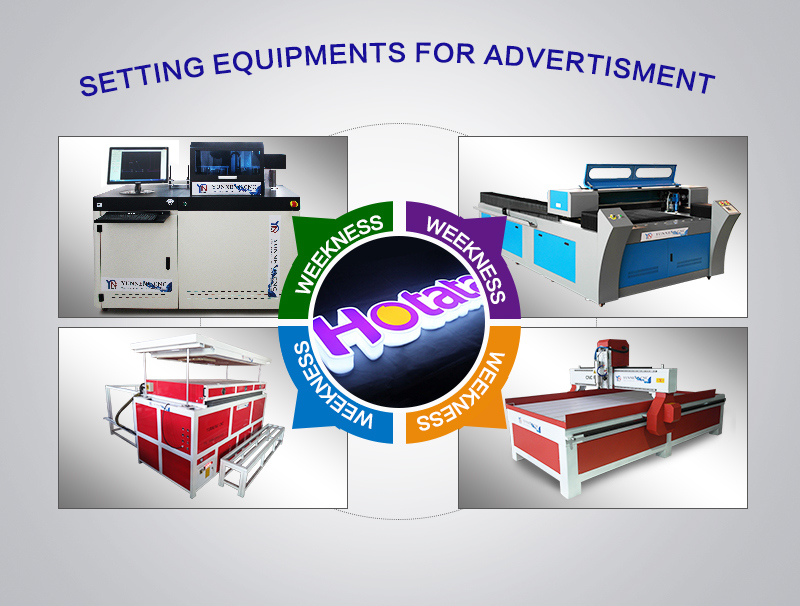
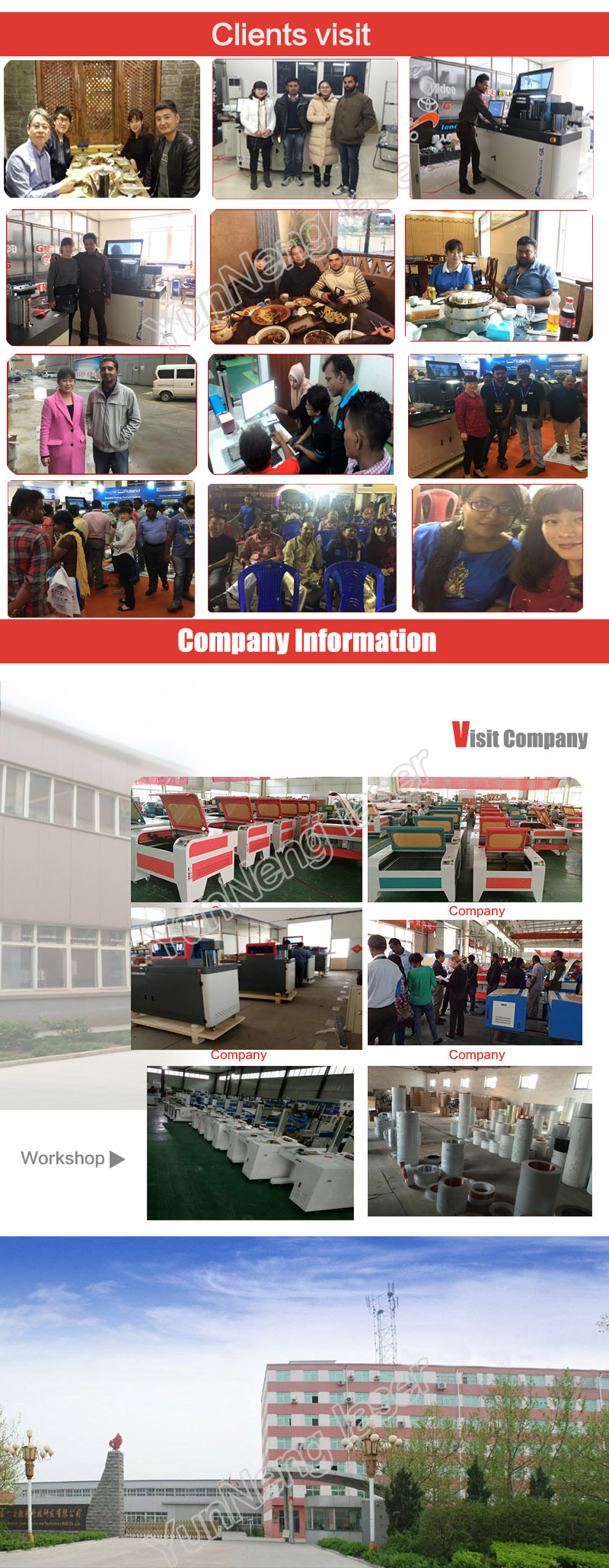
    Thermoforming is a manufacturing process where a plastic sheet is heated to a pliable forming temperature, formed to a specific shape in a mold, and trimmed to create a usable product. The sheet, or "film" when referring to thinner gauges and certain material types, is heated in an oven to a high-enough temperature that permits it to be stretched into or onto a mold and cooled to a finished shape. Its simplified version is vacuum forming.
In its simplest form, a small tabletop or lab size machine can be used to heat small cut sections of plastic sheet and stretch it over a mold using vacuum. This method is often used for sample and prototype parts. In complex and high-volume applications, very large production machines are utilized to heat and form the plastic sheet and trim the formed parts from the sheet in a continuous high-speed process, and can produce many thousands of finished parts per hour depending on the machine and mold size and the size of the parts being formed.
Thermoforming differs from injection molding, blow molding, rotational molding and other forms of processing plastics. Thin-gauge thermoforming is primarily the manufacture of disposable cups, containers, lids, trays, blisters, clamshells, and other products for the food, medical, and general retail industries. Thick-gauge thermoforming includes parts as diverse as vehicle door and dash panels, refrigerator liners, utility vehicle beds, and plastic pallets.
In the most common method of high-volume, continuous thermoforming of thin-gauge products, plastic sheet is fed from a roll or from an extruder into a set of indexing chains that incorporate pins, or spikes, that pierce the sheet and transport it through an oven for heating to forming temperature. The heated sheet then indexes into a form station where a mating mold and pressure-box close on the sheet, with vacuum then applied to remove trapped air and to pull the material into or onto the mold along with pressurized air to form the plastic to the detailed shape of the mold. (Plug-assists are typically used in addition to vacuum in the case of taller, deeper-draw formed parts in order to provide the needed material distribution and thicknesses in the finished parts.) After a short form cycle, a burst of reverse air pressure is actuated from the vacuum side of the mold as the form tooling opens, commonly referred to as air-eject, to break the vacuum and assist the formed parts off of, or out of, the mold. A stripper plate may also be utilized on the mold as it opens for ejection of more detailed parts or those with negative-draft, undercut areas. The sheet containing the formed parts then indexes into a trim station on the same machine, where a die cuts the parts from the remaining sheet web, or indexes into a separate trim press where the formed parts are trimmed. The sheet web remaining after the formed parts are trimmed is typically wound onto a take-up reel or fed into an inline granulator for recycling.
Most thermoforming companies recycle their scrap and waste plastic, either by compressing in a baling machine or by feeding into a granulator (grinder) and producing ground flake, for sale to reprocessing companies or re-use in their own facility. Frequently, scrap and waste plastic from the thermoforming process is converted back into extruded sheet for forming again.
Air Conditioner Bearing
Air Conditioner Bearing,Chrome Steel Air Conditioner Bearing,Large Stock Air Conditioner Bearing
Tai Shi Te Bearing Co., Ltd , http://www.jnballBearing.com