In May 2015, China Truck Network reporter learned from Chai Yongquan, Chief Engineer of Cummins Emissions Control China, that the future diesel exhaust aftertreatment system will have many features such as low cost, high performance, and integration.
This information does not seem to be consistent with the market information we currently recognize. Judging from the current market conditions, each upgrade of emission standards will increase the price of vehicles. Regardless of whether it is a manufacturer or a distributor, the information returned is that the upgrade of the exhaust after-treatment system leads to an increase in the price of the vehicle. In the face of the current market environment and reality, what kind of means does Cummins take to reduce the production cost of the post-processing system?
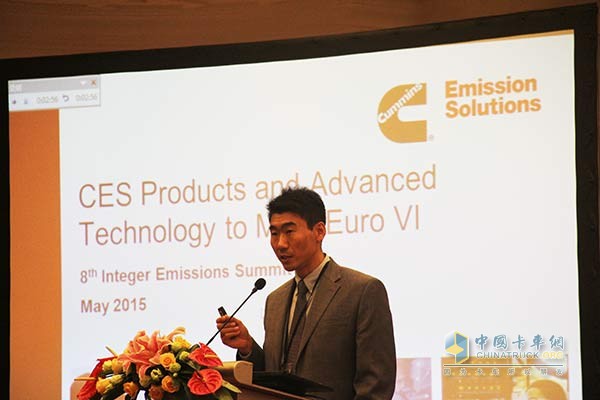
Cummins Emissions Control - China Chief Engineer Chai Yongquan
Although the aim is to reduce prices, Cummins' post-processing system has no intention of reducing quality. Compared with the existing post-processing system, the future Cummins post-processing system will be more scientific and have a higher degree of integration. Xiao Bian will take you to see what future reprocessing has and what advanced design:
Scientific design
Chief Engineer Chai said that the design of the post-processing system is not just a simple metal-coated catalyst carrier coating. A high-quality, high-efficiency post-processing system requires many basic scientific theories such as fluid mechanics, applied mechanics, and thermodynamics to support it. The Cummins Exhaust Aftertreatment System fully considered the urea solution's characteristics of upwind crystallization in the injection process during the design of the urea supply line and the urea nozzle. The closed-loop control system consisting of multiple sensors adopted by them can greatly improve urea catalysis. The efficiency does not cause the secondary pollution of ammonia to the atmosphere caused by the phenomenon of excessive spraying of urea.
Integrated control
In the four national and national discharge phases, multiple components such as nitrogen oxide sensors, temperature sensors, pressure sensors, and urea nozzles will be added to the tail gas after-treatment system. How to accurately control each electronic component to achieve full conversion of pollutants without wasting urea and causing NH3 pollution based on engine operating conditions, temperature, flow rate, and distribution of nitrogen oxides in the exhaust pipe, is the production of tail gas emission treatment system Manufacturers face a common problem. Cummins adopted the CES post-processing system. Different from the conventional post-processing system, it not only controls the engine according to the signal fed back by a nitrogen oxide sensor, but also comprehensively judges according to the signals of multiple sensors such as engine intake temperature, intake pressure, and pressure difference before and after DPF. Correct the urea injection volume to ensure the work efficiency of the post-processing system.
Road experience accumulation
Since the implementation of the North American EPA 07 emission standard in 2007, Cummins has launched the DPF particle trap that is required for the national five emission phase. After many years of practical application experience, the company is already fully aware of the failure modes and coping strategies of the DPF. The post-processing system produced by Cummins not only guarantees the lowest failure rate, but also can solve sudden problems quickly and promptly.
Since the quality has not decreased, then how does Cummins achieve the reduction of product prices? In fact, it benefits from the following aspects:
Global Marketing Strategy
Cummins Emissions Processing Systems Co., Ltd. has a total of seven major engineering centers in five countries in the world. In terms of product production, Cummins focused on road test data that has been accumulated, and used experimental centers distributed by various countries to establish targeted data models based on the characteristics of localization. With the purpose of being most practical, Cummins removed common elements that did not meet regional characteristics. The most suitable low cost product for the product is sold. In the procurement of accessories, Cummins is sourcing globally to ensure product quality while guaranteeing the lowest purchase cost. In terms of product sales, we will use neighboring countries and regions as the center of major production countries to provide products with strong adaptability and low sales prices at the same time, and at the same time, reduce the cost of spare parts logistics transportation and bring benefits to users.
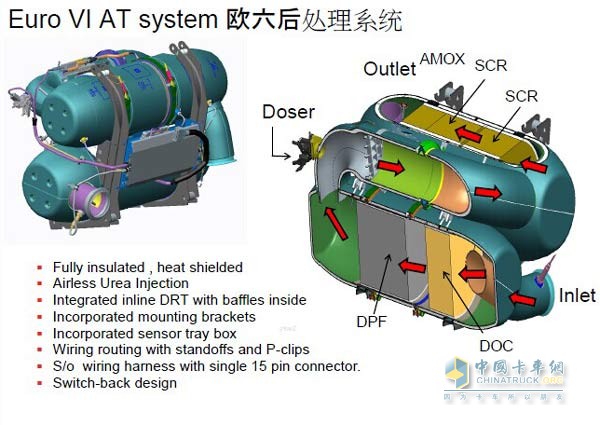
Cummins Euro VI post-processing system
Universal product design
In terms of product integration design, Cummins adopted an integrated design of the DOC/DPF/SCR post-processing system to minimize the volume of the post-processing system. The use of a rotatable inlet exhaust port design can be applied to most vehicle models. With its low-cost, general-purpose features, it can increase market share and reduce the average development cost of each product.
From the product design idea we can see that the future Cummins Exhaust Gas Treatment System will move towards the intelligent, integrated and universal production and marketing road.
Buy truck parts, on the Taobao stalls, multiple discounts waiting for you to take!
Http://Drain.html
We have three models Emulsion plant:GYRY06F(without heating system ) ,GYRY06H ,GYRY10B.
Series asphalt emulsion plant adopts the structure of a container, which makes it easy to be transferred between different construction sites. With an efficient heat exchanger and automatic control system, the asphalt production machine is able to produce all kinds of asphalt emulsions at high efficiency.
Technical Parameters
Model: GYRY06H
Total power: 30kW
Emulsifier speed: 2900rpm
Emulsifier power: 15kW
Heating power for heat transfer oil: 9kW
Burner power: 10×10â´kCal/h
Heat transfer area: 15m²
Emulsified asphalt fineness: <5μm
Production capacity: 6t/h
Weight: 4.5t
Dimension: 4700×2150×2330mm (L×W×H)
Technical Parameters
Model: RY10B
Max capacitance: 60kW
Emulsifier power: 30/22kW
Emulsifier speed: 2930r/min
Heating power for heat transfer oil: 9kW
Heat transfer area: 27㎡
Emulsified asphalt fineness: <5μm
Capacity: 10t/h
Weight: 6t
Burner power: 20×10â´kcal/h
Dimension: 6500×2300×2700mm (L×W×H)

Emulsion Asphalt Plant
Emulsion Asphalt Plant,Bitumen Emulsion Plant,Automatic Emulsion Asphalt Plant ,Asphalt Emulsion Machine Plant
Henan Gaoyuan Road Maintenance Equipment Co., Ltd. , https://www.sgroadmachinary.com